Traceability, Inspection and Test Certification
Introduction
CRP believes that product traceability is a valuable feature of finished products when one is serving markets with both process and safety critical items. From a process perspective the customer often wants confidence in knowing the materials of construction and that the supplier has undertaken certain materials testing. In order to obtain proof of materials and testing, customers often request materials certification for product. Whilst CRP are capable of and often do provide such certification, the business set out some time ago to try to eliminate this costly and essentially “non-value added activity” whilst still providing the ability to prove materials and testing. Similarly, if for any reason a product fails in service, it is often valuable to trace its manufacture and test as part of the investigation into the cause of failure. For these reasons CRP has developed a comprehensive system for tracing product back through its manufacturing tests and processes to the raw materials without needing to burden the customer with the cost and management of documentation. All of our manufacturing processes and test procedures fall within our ISO9001:2015 accreditation and all products are designed and manufactured to comply to the Pressure Equipment Directive and are CE marked where applicable. Our two principal lining procedures involve paste extruded PTFE and PFA moulded components.
PTFE Lined Piping
Lined piping is produced through a number of manufacturing and test stages—see the diagram below.
Raw Materials
CRP purchase PTFE fine powders from well known global manufacturers, the fluoropolymer is delivered in 25kg tubs, each marked with the manufacturers batch reference. This batch reference represents one lot in terms of product testing and manufacturer’s test results refer to this batch number. Similarly the isoparaffin used as a processing aid is also linked through a batch number to its materials test certificate.
Mixing
Precise amounts of PTFE and isoparaffin are mixed cold. A mixing log records the amounts of each material used, the mixing conditions, operator and batches used. The key data is also placed on a label on each mixed tub of material.
Extrusion
After warm conditioning the material is selected for extrusion and the data collected from the material tubs and mixing log is transferred to the extrusion record sheet. Each batch of a particular PTFE liner size—bore and wall thickness has an extrusion record sheet created for it. At this stage an extrusion reference is allocated to the batch and entered on the extrusion record sheet in the format shown below.
For example the second batch of the day on Wednesday, week 45, 2012 made on extruder E would have the reference E23452.
Sintering
The extrusion record sheet accompanies the oven sintering process and holds all of the extrusion data, mixing data and that relating to the sinter cycle. During the sinter cycle an oven trace is recorded, and this is put with the extrusion record sheet. After sintering each length of liner is marked with the extrusion reference, and a test piece is taken to the test room together with the extrusion record sheet and oven trace.
Test
Mechanical properties are tested for each test piece, both ultimate tensile strength and elongation at break. This is undertaken for ten samples from the test piece, five in the longitudinal direction and five in the cross direction. The specific gravity of the test piece is calculated and dimensional checks made. These records are held against the extrusion reference and all our testing meets the requirements specified in ASTM F423.
Pipe Lining
When a length of liner is selected for inserting into the steel pipe the liner reference is hard stamped onto one flange of the pipe spool.
Finished Spool
The finished pipe spool is subject to a 29 bar hydrotest for 3 minutes conducted twice and for virgin PTFE an electrostatic test at 25kVa to ensure the integrity of the liner. These test results are recorded against both the customer order reference and the extrusion reference.
PFA Lined Fittings
Lined fittings have fewer manufacturing stages than PTFE lined pipe—see the diagram below.
Raw Materials
PFA is delivered in 25kg tubs, each marked with the manufacturers batch reference. Again this represents one lot in terms of product testing and material certificates provided by the manufacturer and their test results refer to this batch number.
PFA Testing
The PFA we use meets the requirements of ASTM D3307 Type 2. They are also specified as having a restricted melt flow index not exceeding 3 grammes in 10 minutes.
We extensively use our own in house melt flow indexing test equipment to ensure the PFA complies to these strict quality controls.
Moulding
Specific batches of material are used for moulding and no two batches are ever mixed. A moulding record sheet identifies the batch number of polymer and allocates a simple sequential reference, preceded by the letters PFA and followed by a two digit year as below.
For example the 1456th moulding made last year would be PFA 1456 11.
Trimming
The finished moulding is stripped from it’s tooling and trimmed.
Test
Following a visual inspection the component is subject to an electrostatic test at 25kV and a hydrotest at 29 bar for 3 minutes conducted twice. At this point the component is stamped up with its mould reference. The test results are entered onto the moulding record sheet.
When every lined item has passed a hydrotest one of the flanges is hard stamped with a waterdrop symbol to confirm the test.
When every lined item has passed an electrostatic test one of the flanges is hard stamped with a lightening symbol to confirm the test.
Conclusion
This method of product identification enables product in the field to be married up with the product materials and test records in the event of any concern or required investigation; without putting the onus on the customer to find paper based records and try to reconcile them against physical plant.
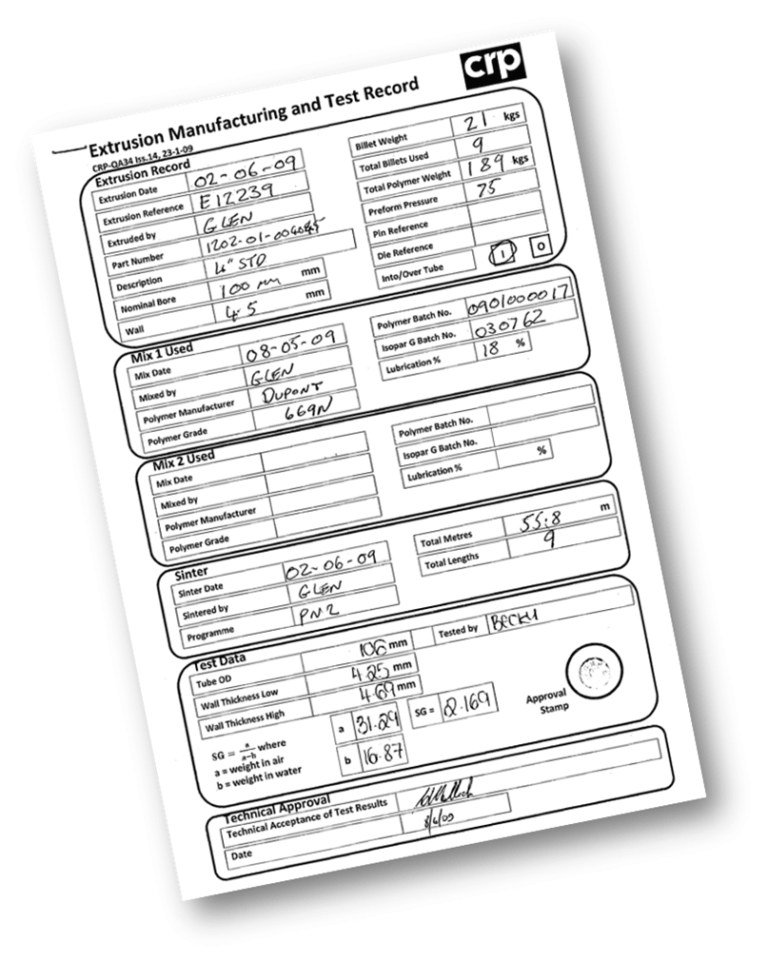